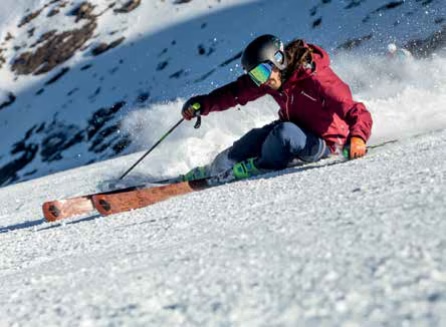
langlebigen Unikat viele Jahre treu bleiben I © Ünique/Bernhard Fiedler
DAS ABENTEUER IST DIE REISE – und an deren Ende steht ein Partner, auf den man abfährt. Der erste Teil dieses Satzes stammt von Dominic Haffner, seines Zeichens Eigner und Seele der Ski-Manufaktur Ünique. Hier werden Ski produziert, deren einzige gemeinsame Eigenschaft „hochwertig“ ist. Individuelle Stücke, die sich am Fahrstil und den Erwartungen des Skifahrers orientieren. Handgeschnitzt“ wäre trotz der Holzoberfläche die falsche Formulierung, denn drinnen steckt Hightech pur.
BEGINNEN WIR GANZ UNSPORTLICH AM ZIEL: Der finalen Probe aufs Exempel, wie sich der individuell, auf den eigenen Vorstellungen basierende Ski anfühlt. Unser Plan war, einen pistentauglichen Ski mit viel Spaß auch im nicht perfekten, verspurten Gelände hinzubekommen. Das edle Stück mit einer Oberfläche aus dunklem brasilianischen Pfefferholz und den leuchtenden grünen Wangen erwies sich als gewichtiger, als es die gewählte Länge von nur 174 cm erwarten lassen würde. Nach einem kurzen Gewöhnungsprozess machte das Gerät dann vor allem zwischen Buckeln durchaus Spaß. Aber so richtig topp war das Feeling, wenn es in den teilverspurten Neuschnee ging. Da weiß man, was man gebastelt hat – oder bei weniger persönlichem Einsatz – einem gebastelt wurde. Doch ohnehin steht der spannende Weg zu diesem Ziel für die meisten im Vordergrund, hebt Haffner gerne hervor.
DOCH SEINE FAHRKÜNSTE RICHTIG EINZUSCHÄTZEN – das steht am Anfang dieser Reise, betont Dominic, der diese Reise in den vergangenen zehn Jahren schon mit 120 Skisportlern unternommen hat. Es war sommerlich warm, der Hintertuxer Gletscher zeigte sich von seiner grauen, schneefreien Seite. Exakt zehn Fahrten kratzen wir über die Piste, mit insgesamt vier unterschiedlichen Skiern. Die Basis war gelegt, denn elektronische Sensoren in den Sohlen halfen meine Fahreigenschaften zu analysieren. Noch wichtiger war der mit einer Videocam bewaffnete Schatten Dominic. Insgesamt waren wenige Stunden vergangen, dann trennten sich die Wege. Umso sensationeller, als wenige Tage später die gesammelte Analyse samt Schlussfolgerungen im Mailordner lagen.
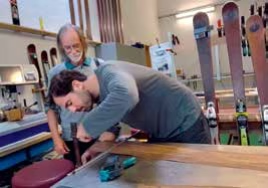
„DIE VIDEOS UND FOTOS habe ich mir noch einmal angesehen und und ich finde, dass Du einen sehr schönen, ruhigen Fahrstil hast. Positiv ist mir die starke Hoch-Tiefbewegung aufgefallen, womit Du deinen Ski zwar einiges an Arbeit abnimmst, aber es natürlich mehr Kraft kostet. Ich habe versucht hier die Arbeit mehr in den Ski zu verlagern, sodass Du mit weniger Kraft auskommst. Aufgefallen ist mir auch eine leichte Rücklage bei deinem Schwung, was ich durch die Bindungsposition in Kombination mit der Außenkontur des Skis und dem Flex minimieren werde. Um Dir den Umstieg auf deinen neuen Boliden nicht zu schwer zu machen habe ich den Radius mit 14 m ein wenig reduziert, er dreht besser und die Mittelbreite von 85 mm für die Tage außerhalb der Piste werden Dir mehr Auftrieb geben, sodass die Powdertage zumindest für kleine Abstecher neben der Piste ein bisschen mehr Spaß machen. Durch die gering höhere Breite stehst Du aber satter auf der Piste und es erhöht die Stabilität des Skis, was sich auch auf die Laufruhe überträgt.“
IN DER WERKSTATT wird aus der Theorie Realität. Zwischen den manuellen Arbeiten gibt Dominic als studierter Physiker und Patentanwalt, der lange die Innovationen heimischer Skiproduzenten in Worte fasste, Einblicke in Details. So sind die Unterschiede zu Skiern aus der Fabrik wirklich markant. Der Belag ist dort 1 bis 1,2 mm dünn, während Ünique 1,8 bis 2 mm dicke Beläge verarbeitet. Gleiches gilt für die Kanten, die dann 2,2 mm erreichen. Ein Teil der Steifheit des Skis kommt von der Stahlkante. Die stärkeren Kanten machen den Ski länger haltbar, verhindern, dass er an Spannung zu rasch einbüßt. „Aber er ist nicht unkaputtbar, obwohl es noch keiner beim Fahren geschafft hat einen der angefertigten Skier zu zerstören“, sagt Dominic. „Sonst sollte ein regelmäßig präparierter Ski 100 Fahrtage überstehen, bei meinen individuell gefertigten Skiern gehe ich von zumindest 200 Skitagen aus. Auch meine ersten produzierten Ski funktionieren noch“, sagt Dominic. Die unfreiwillige Probe aufs Exempel folgte schon am zweiten Skitag, als sich im Gelände ein unter der Neuschneeschicht gut versteckter Fels als Stolperstein erwies. Der Ärger war groß. Ebenso groß war anschließend die Überraschung: Ein leichter Kratzer auf der Kante und eine fast unmerkliche Furche am sonst unbeschadeten Belag – das war alles.
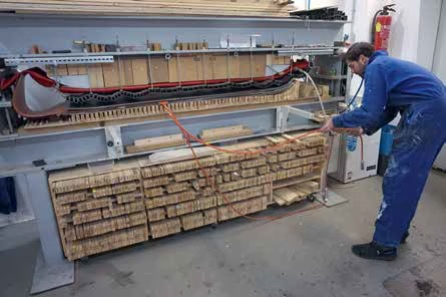
JETZT WIRD DER SKI allmählich dreidimensional. Auf den Belag werden die kunstvoll gebogenen Kanten gelegt, dazu Gummibänder die dämpfen. Es folgt die erste Schicht Flachs, dann Carbon dessen Faserung in der richtigen Richtung gelegt sein muss, sonst wird der Ski zu unruhig. Dann folgt der Holzkern, die nächste Carbonschicht, dann wieder Flachs und schließlich kommt oben das Furnier drauf. Dazwischen darf auch der Amateur fleissig mitarbeiten, wenn Schicht um Schicht mit einer nicht gerade duftenden Epoxymischung laminiert wird. Allmählich wird man eins mit dem Produkt, das vor den eigenen Augen wächst. Zum feierlichen Abschluss – allein diese Tätigkeiten haben vier Stunden beansprucht – kommen die Skier zwischen Alu und Heizmatten. Dann werden sie mühevoll angehoben und in die Presse gehievt. Auf den Millimeter genau muss alles eingepasst werden, damit Biegung und Steifheit den am Computer errechneten Daten entsprechen. Dann werden die Matten auf 45 bis 50°C erhitzt.
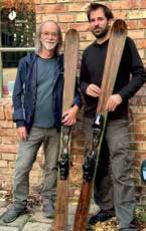
ES IST VOLLBRACHT, ein erhebendes Gefühl, Feierstimmung! Rund 6.000 Euro kostet der Spaß, doch Dominic weiß: Bei allen seinen Kunden treten in dem Moment, wo die Ski in der Presse waren – oder spätestens, wenn sie nach mehreren Bearbeitungsgängen schleifen und polieren endlich übernommen werden konnten – die Kosten in den Hintergrund. Denn spätetens nach den ersten Schwüngen ist man endgültig eins mit den neuen Brettln.