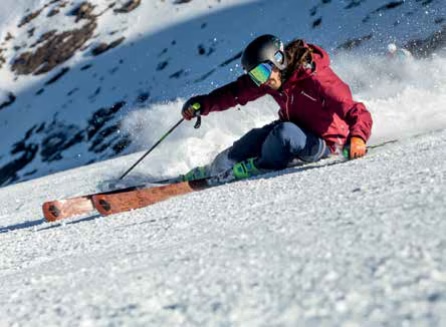
long-lasting unique piece that will remain true to itself for many years I © Ünique/Bernhard Fiedler
THE ADVENTURE IS THE JOURNEY – and at the end of it there is a partner you love. The first part of this sentence comes from Dominic Haffner, the owner and soul of ski manufacturer ÜniqueHere, skis are produced whose only common characteristic is "high quality". Individual pieces that are geared to the skiing style and expectations of the skier. Despite the wooden surface, "hand-carved" would be the wrong wording, because inside there is pure high-tech.
LET'S START WITH THE GOAL IN A VERY UNSPORTY WAY: The final test of how the ski feels, based on your own ideas. Our plan was to create a ski that is suitable for the slopes and that is also fun to use in imperfect, tracked terrain. The elegant piece with a surface made of dark Brazilian pepperwood and bright green cheeks turned out to be heavier than the chosen length of just 174 cm would suggest. After a short period of getting used to it, the device was a lot of fun, especially between bumps. But the feeling was really great when we went out into the partially tracked fresh snow. Then you know what you have made - or, with less personal effort, what was made for you. But anyway, the exciting path to this goal is the main focus for most people, Haffner likes to emphasize.
BUT CORRECTLY ASSESSING HIS SKILLS – that is the beginning of this trip, emphasises Dominic, who has already undertaken this trip with 120 skiers over the past ten years. It was summery warm, the Hintertux Glacier showed its grey, snow-free side. We made exactly ten runs down the slopes, with a total of four different skis. The basis had been laid, as electronic sensors in the soles helped to analyse my skiing characteristics. Even more important was Dominic's shadow, armed with a video camera. A few hours had passed in total, then we parted ways. All the more sensational when a few days later the collected analysis and conclusions were in the email folder.
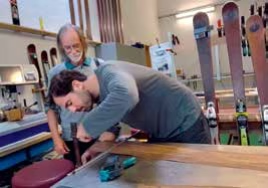
"I've looked at the videos and photos again and I think you have a very nice, calm skiing style. I noticed the strong up-down movement, which means you take a lot of work off your skis, but of course it takes more energy. I've tried to shift the work more into the skis so that you can get by with less energy. I also noticed a slight backsliding in your turns, which I will minimize by adjusting the binding position in combination with the outer contour of the ski and the flex. In order not to make the transition to your new racer too difficult for you, I've reduced the radius a little to 14 m, it turns better and the middle width of 85 mm for the days off the piste will give you more lift, so that the powder days are a little more fun, at least for short excursions off the piste. The slightly higher width means you stand more firmly on the piste and it increases the stability of the ski, which also transfers to the smoothness of the ride."
IN THE WORKSHOP, theory becomes reality. Between the manual work, Dominic, a trained physicist and patent attorney who has long put the innovations of domestic ski manufacturers into words, provides insights into the details. The differences to skis from the factory are really striking. The base is 1 to 1.2 mm thin, while Ünique uses bases that are 1.8 to 2 mm thick. The same applies to the edges, which then reach 2.2 mm. Part of the stiffness of the ski comes from the steel edge. The stronger edges make the ski last longer and prevent it from losing tension too quickly. "But it is not indestructible, although no one has yet managed to destroy one of the skis made while skiing," says Dominic. "Otherwise, a regularly prepared ski should last 100 days of skiing; with my individually made skis, I expect at least 200 days of skiing. Even my first produced skis still work," says Dominic. The involuntary test came on the second day of skiing, when a rock well hidden under the layer of fresh snow turned out to be a stumbling block. The frustration was great. The surprise afterwards was just as great: a slight scratch on the edge and an almost imperceptible furrow on the otherwise undamaged surface - that was all.
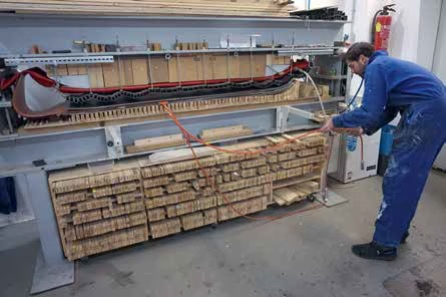
NOW THE SKI IS GRADUATELY BECOMING 3D. The artfully curved edges are placed on the base, along with rubber bands for dampening. The first layer of flax follows, then carbon, the fibers of which must be placed in the right direction, otherwise the ski becomes too unstable. Then comes the wood core, the next layer of carbon, then flax again, and finally the veneer is placed on top. In between, even amateurs can work hard as layer after layer is laminated with an epoxy mixture that doesn't exactly smell good. Gradually, you become one with the product that is growing before your eyes. At the ceremonial end - these activities alone took four hours - the skis are placed between aluminum and heating mats. Then they are laboriously lifted and hoisted into the press. Everything has to be fitted to the millimeter so that the bending and stiffness correspond to the data calculated on the computer. The mats are then heated to 45 to 50°C.
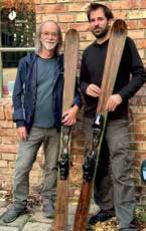
IT'S DONE, an uplifting feeling, a celebratory mood! The fun costs around 6,000 euros, but Dominic knows that for all of his customers, the costs fade into the background as soon as the skis have been in the press - or at the latest when they can finally be taken over after several processing steps of grinding and polishing. Because after the first few turns, at the very latest, you are finally one with the new skis.